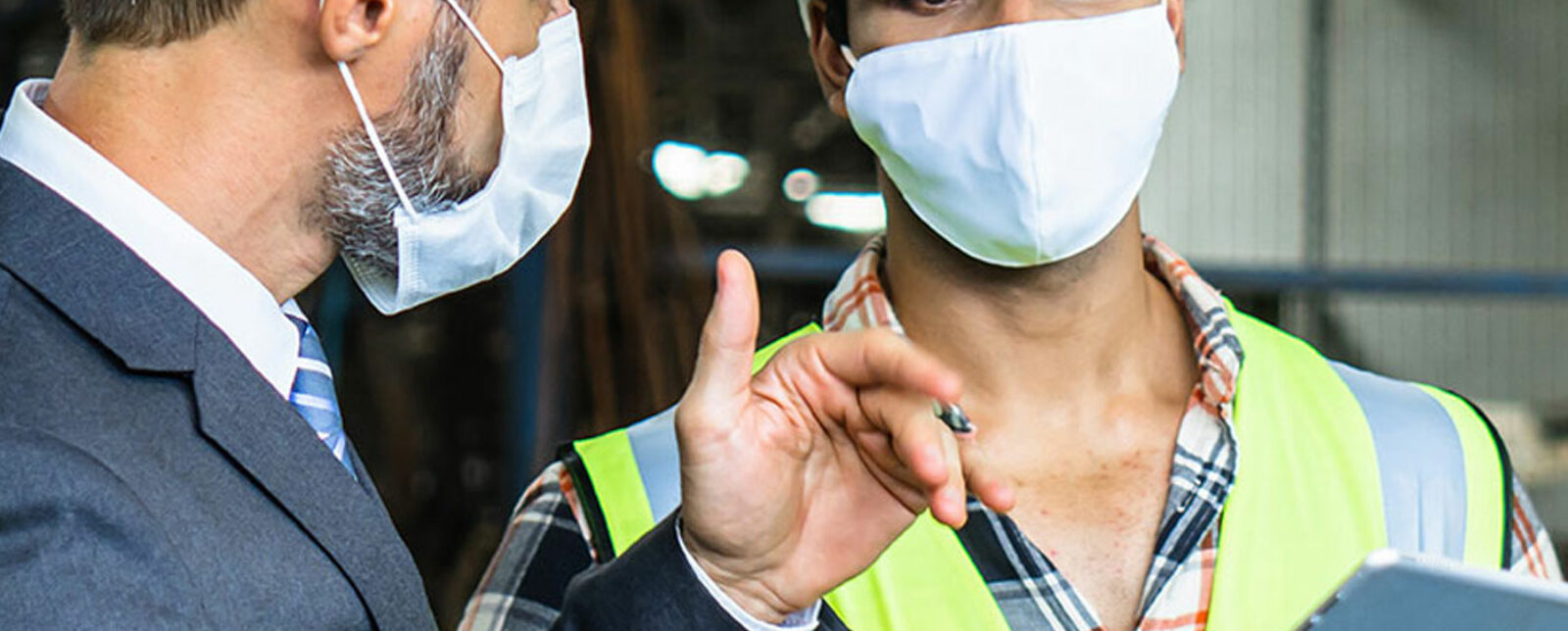
Introducing the Kaizen Booster Approach
Kaizen-Booster can be part of Operational Excellence programs as a real lever to revitalize teams. The Kaizen-Booster is activated and animated in agile mode in the same way as an Andon type action (during a quality drift). The Kaizen-Booster project will use the Lean tools (TPM, 5S, Flow diagram, process analysis, SMED, etc.) to lead the reflections, analyzes, research and implementation of solutions.
From a Tactical and Operational Standpoint
Who is Concerned?
The Kaizen Booster approach is deployed on a targeted work area such as a UAP or a process (vertical or transverse).
The Composition of the Group
In general, the participants are an inter-functional team: management controller, maintenance staff, UAP manager, production operators, marketing, sales …
Procedure
The collective spends five to six days in the target area – that is to say mainly in the field – to study the process, collect and analyze data, discuss options for improvement and implement concrete changes – which may involve moving or modifying equipment and processes.
The Kaizen Booster is led by Operational Excellence or by an internal coach. We will recommend animation with collective intelligence to maintain the balance between production and emotion, between content and relationship.
This mode of animation will thus make it possible to accelerate the adhesion and the sharing within the group which carries the stakes of results.
Methodology
A site, three phases:
- Validation of the targeted process & qualification of the expected performance (1 day).
- Workshops with the collective to characterize the issues and identify solutions (3 to 5 days).
- Capitalization and capillarity on the impacts (1 day).
Teams will be part of a continuous improvement loop as they appropriate the first gains.
Expected Benefits
- Revitalize losing Lean programs
- Reduce recurring or contextual irritants
- Speed up the treatment of underperformance (lead time, yield, etc.)
- Eliminate waste within support processes
- Digitize part of your activities (touchscreen tablet, IOT, etc.)
- Instruct the use cases to be launched with Artificial Intelligence
Not to be Confused
The objective of a Kaizen Booster is not to create a perfect UAP (or process), but to initiate visible, measurable and lasting improvements in a short time with iso resources and iso budget.
Phase 1: Validation & Qualification
Validation of the Targeted Process and Qualification of the Expected Performance
Irritants / Performance Jumps
During the routines, the operational teams and the management identify the irritants and the performance jumps sought in a specific process.
Stakes and Objectives
An Operational Excellence facilitator or internal coach validates the challenges and expected objectives with the teams. He co-built a multidisciplinary team to lead the Kaizen Booster project.
KPI Indicators
They make it possible to measure the under-performance addressed as well as the time mesh necessary for a coherent statistical measurement (depending on the activity and the process).
Digital Tools
They are quick and easy to deploy to collect and analyze data (real decision support for operational staff) by relying on the KEPLER ecosystem (eg: Declique, Usitab, etc.).
We recommend the creation of a collective with varying levels of maturity on operational excellence and process control.
Phase 2: Implementation
The teams are trained in the use of measurement tools, which are configured with their help. The field measurements are initialized then tested.
The information is analyzed day by day during field workshops around classic Lean tools to eliminate dysfunctions.
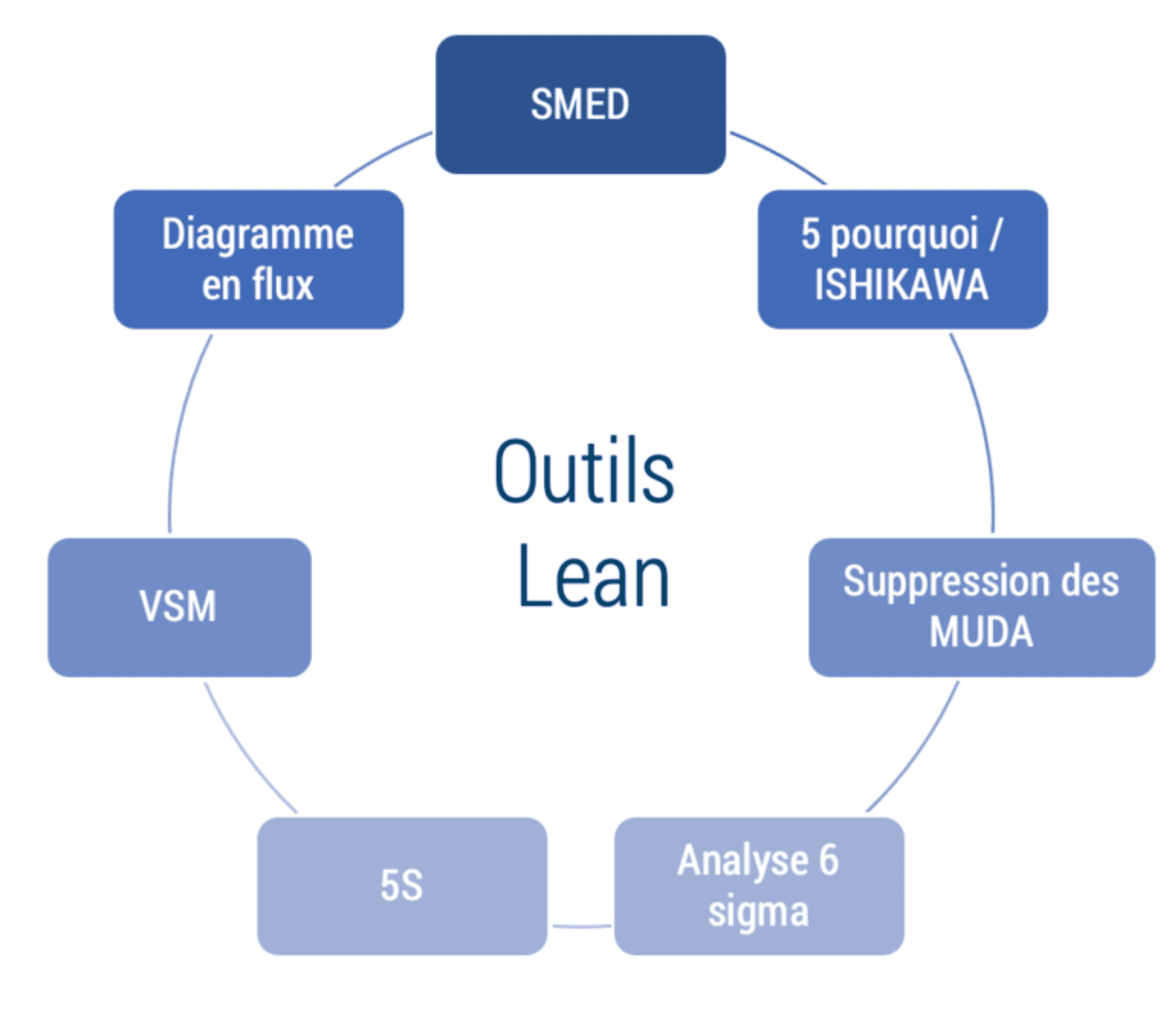
Methodology
The list of actions is reviewed & prioritized, in the short, medium or long term, before being shared with the teams:
- Only short-term actions are implemented in order to show the effectiveness of the approach,
- Prioritization is made through the estimated gains,
- The tools are digitized to allow more efficient deployment and learning All the data is formalized on a dashboard allowing management teams to follow the progress of actions after interventions.
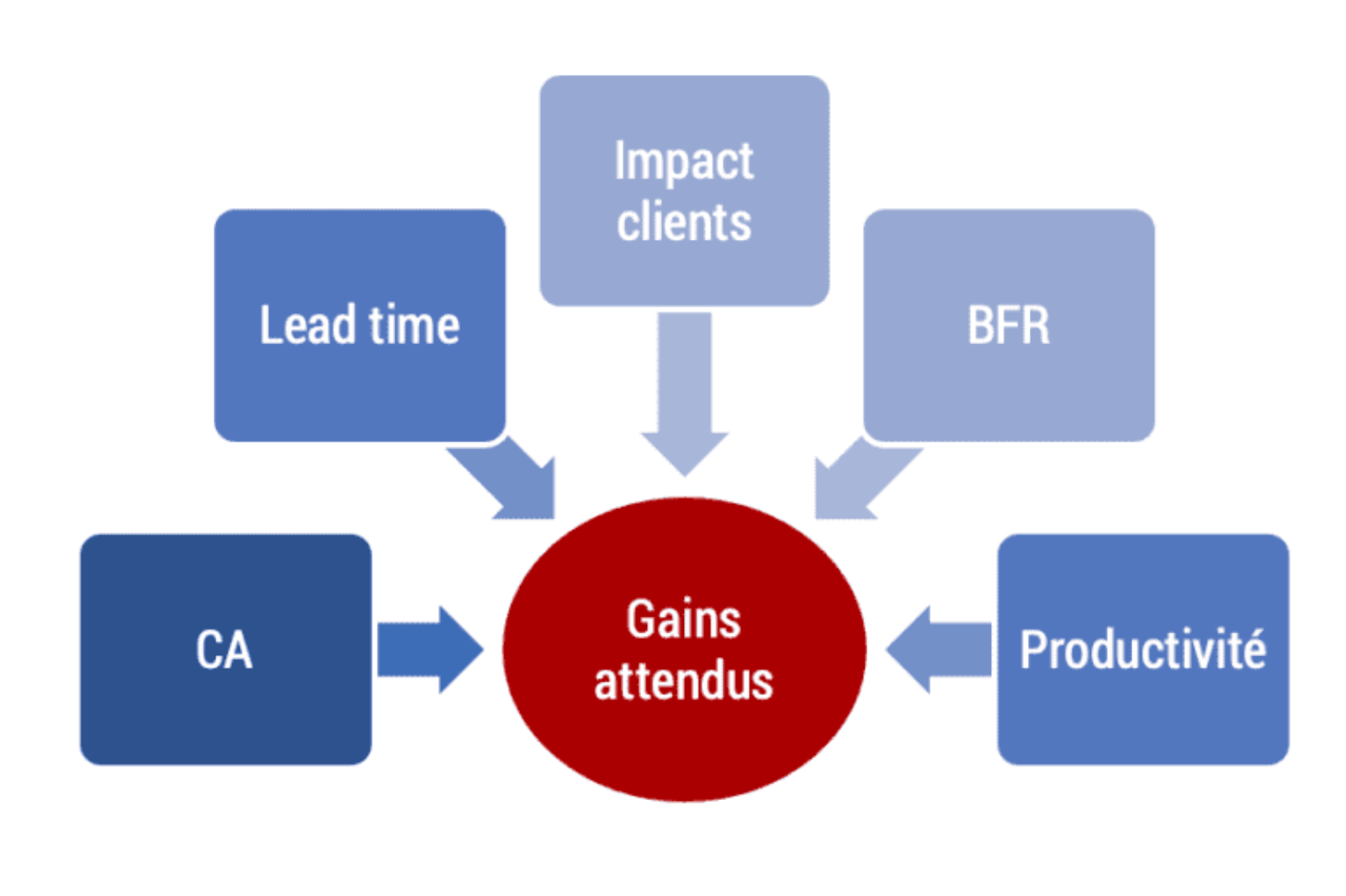
Phase 3: Capitalization & Capillarity
Capitalization
The team and a member of CODIR are conducting a review on the UAP to illustrate the effectiveness of the changes and the measures undertaken, the appropriation of the approach by the operational staff, the initial results and impacts on the Quality / Cost / Time triptych and the next routines aimed at sustaining the gains made.
Capillarity
Finally, to initiate the appropriation by other UAPs or process owners of the Kaizen Booster approach, an employee who has identified a performance subject will be invited to the capitalization session. The collective will then present the approach adopted and the results obtained.
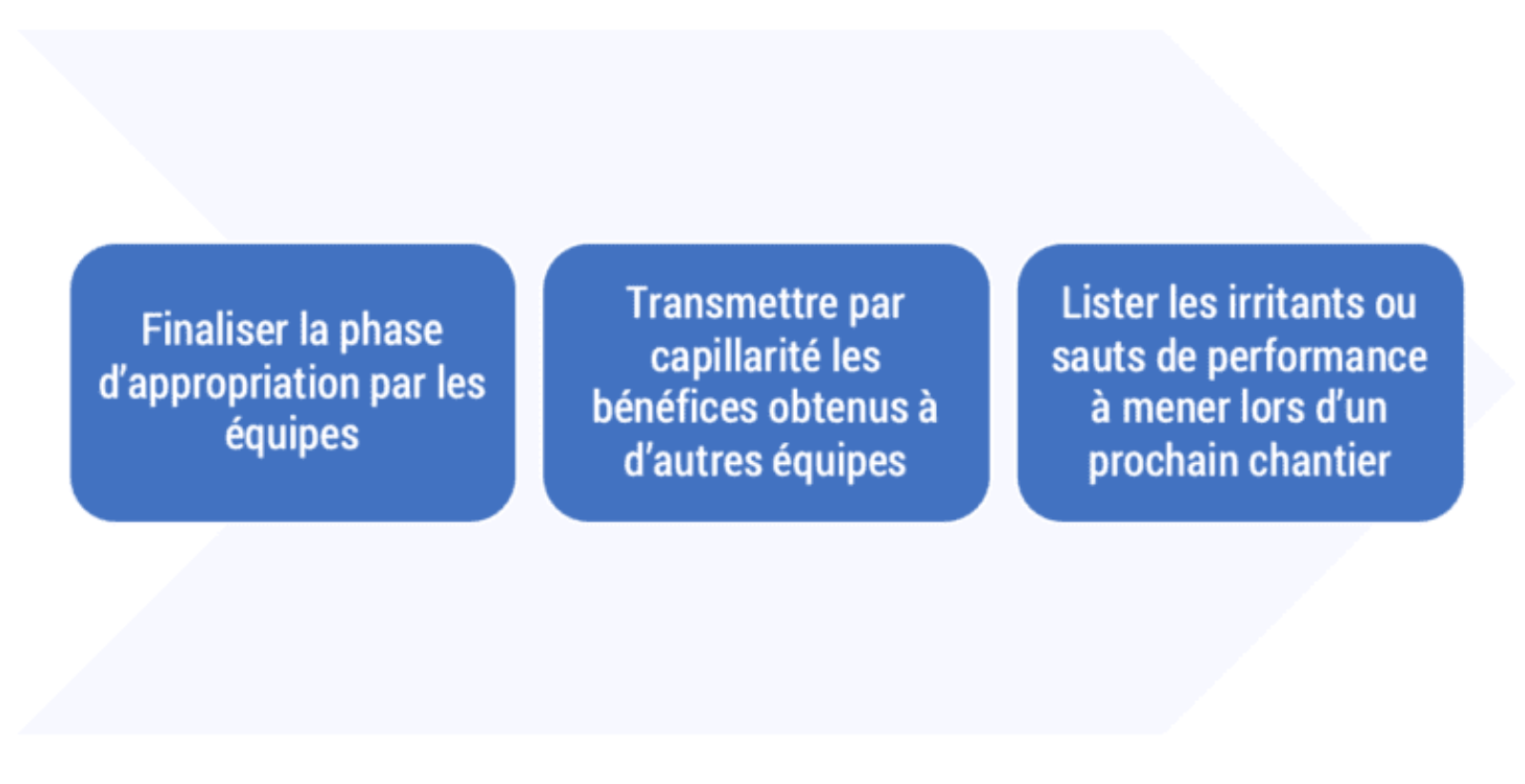
Fast results
The Kaizen Booster approach can be deployed quickly and produce measurable results within 2 to 3 weeks. It supports the actions and performance activities underway in your company.
It also allows to instruct, if relevant, a use case to be carried out around Artificial Intelligence and available data in order to go even further in performance.
Three Foundations for a Successful Deployment
1 / Collaborate With the Field Teams Within Several Departments
The greatest losses are found at the interfaces of the professions: Quality – maintenance – production – logistics, etc., and are suffered and detected by the operators.
The use of digital solutions will make it possible to quantify the losses or underperformance which are often poorly dimensioned while the impact on the PRI (Industrial Revenue Price) is often substantial.
2 / Support the Implementation
Once the dysfunctions have been quantified and validated, it is imperative to work with the field to identify and implement the solutions that they will appropriate.
The short duration of the Kaizen Booster project makes it possible to effectively mobilize employees within a team collectively committed to a dynamic of tactical and then operational transformation.
3 / Create a Collective
The Operational Excellence facilitator will look for interfaces to create links with complementary expertise if necessary. It will then stimulate interactions through collaborative tools with multisite or teleworking teams.
Finally, exchanges, co-construction and common culture are the recognized bases of a successful collective intelligence approach.
To Deepen the Discussion on the Kaizen Booster
Downloadable Version
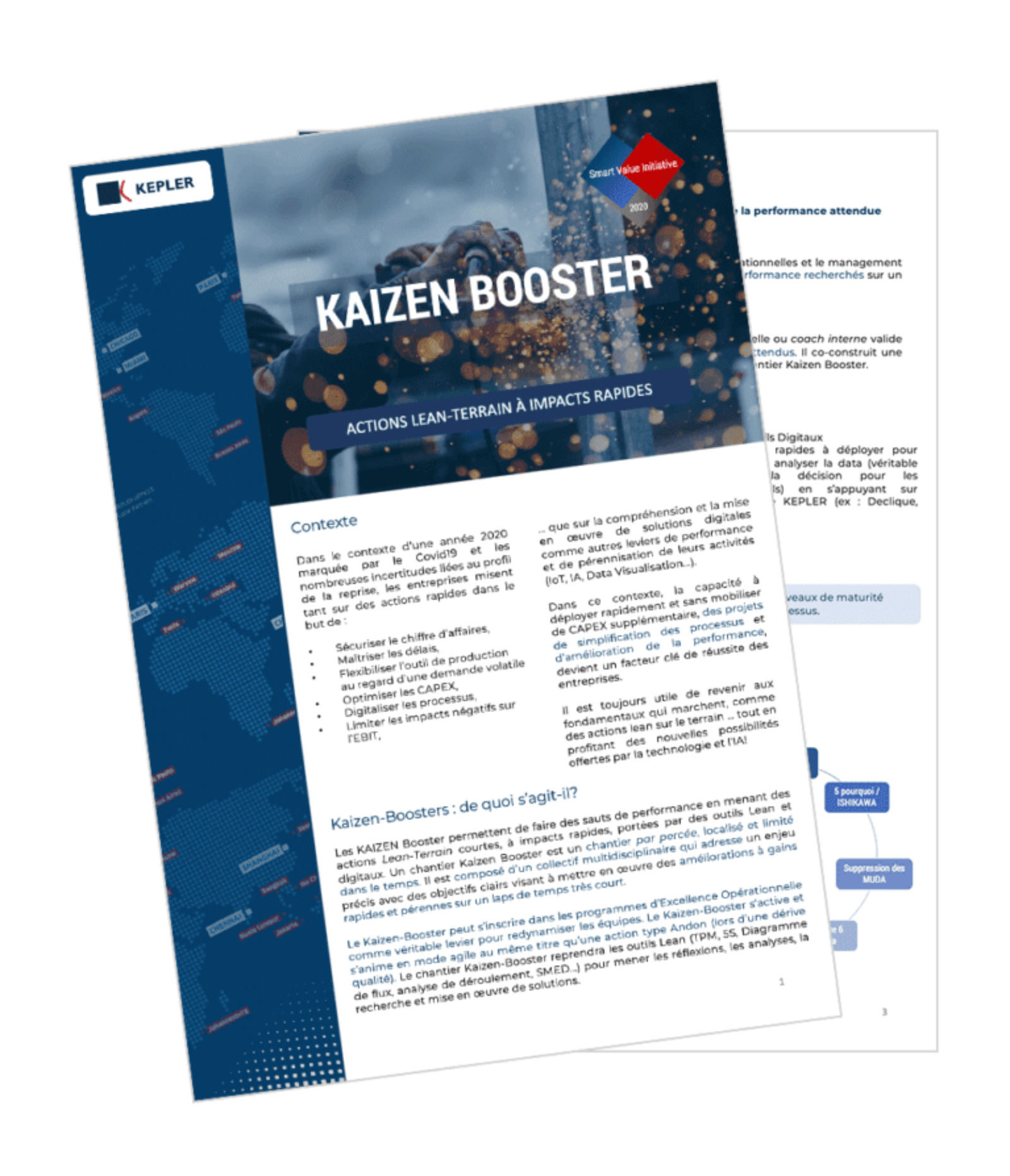
The Three Possible Types of Intervention
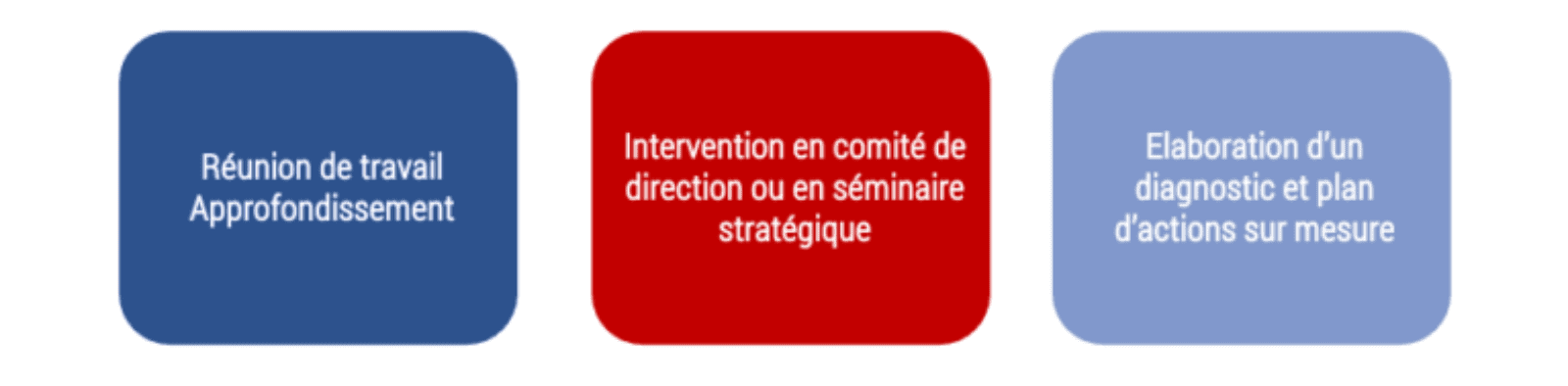