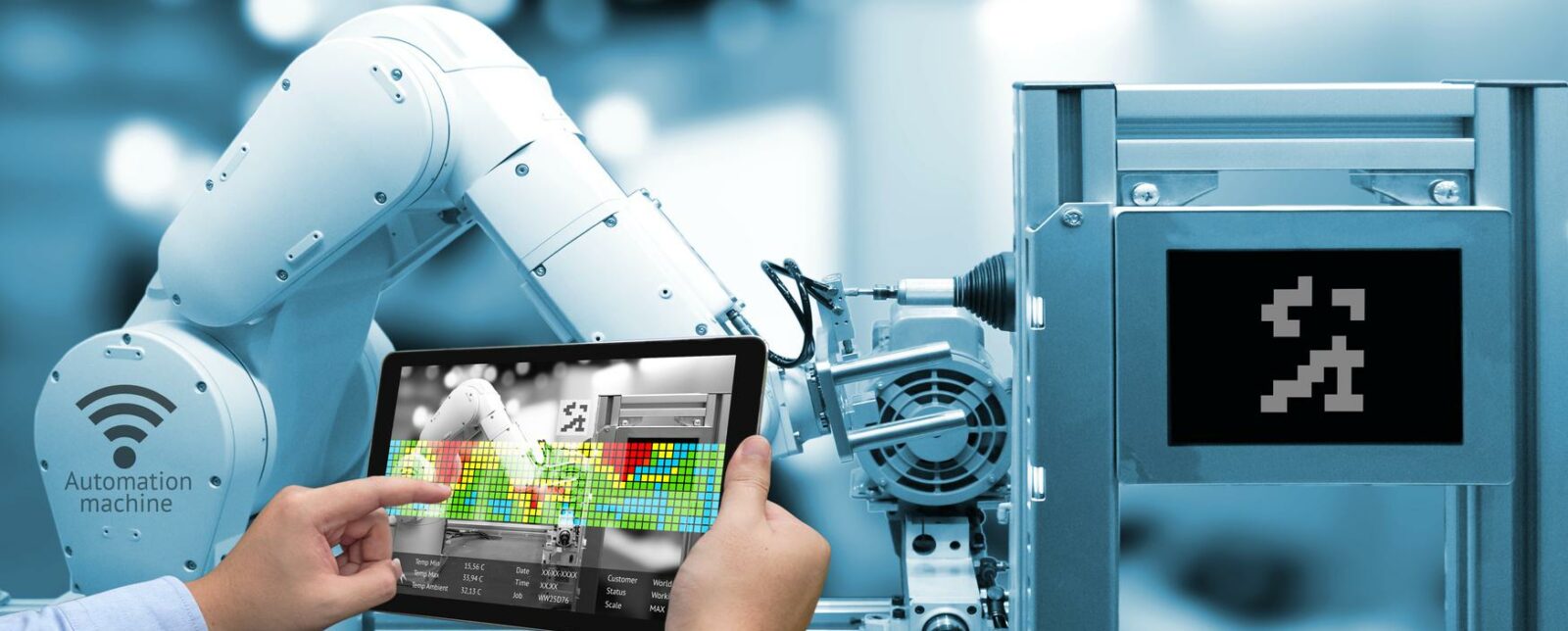
Total Productive Management (TPM) et technologies de l’industrie 4.0 : état des lieux
L'objectif du Total Productive Management ou TPM
L’Overall Equipment Efficiency (OEE) recense classiquement 16 pertes d’efficacité qu’elle répartit au sein de trois groupes :
- les pertes liées à l’équipement,
- les pertes liées à la main d’œuvre
- les pertes liées aux matières, à l’outillage et à l’énergie.
L’objectif du Total Productive Management est d’assurer une réduction systématique de ces pertes.
Cette démarche a été énoncée pour la première fois par le JIPM (Japan Institute for Plant Maintenance) en 1989. Elle se base sur huit piliers,
Les huit piliers de la démarche TPM - Total Productive Management
Gestion et maintenance autonome des équipements
C’est la partie de la maintenance prise en charge par les opérateurs de la production pour rendre plus autonomes et flexibles les unités de production. Deux types d’activité dans la maintenance autonome (MA) : les routines quotidiennes (inspection, nettoyage, contrôle de fonctionnement, gestion du poste de travail (approvisionnements, déclarations, …)) et le traitement des aléas (redémarrages, détection d’anomalies, traitement d’aléas, réparations définies). Le déploiement de la MA comporte 7 étapes.
Elimination des gaspillages / Améliorations au cas par cas
Sont visés tous les gaspillages et causes de perte d’efficience. La recherche et l’élimination de la cause racine par des activités d’amélioration (Kaizen) doit éliminer définitivement les dysfonctionnements.
Maitrise ou maintenance de la qualité
L’objectif est d’éliminer les causes de non qualité sur les produits afin d’atteindre le zéro défaut.
Maintenance planifiée
C’est la partie de la maintenance prise en charge par les techniciens, il existe différents niveaux : le curatif, le préventif et le prédictif. La planification vise à augmenter le MTBF (Mean Time Between Failures), à réduire le MTTR (Mean Time to Repair), à gérer les pièces de rechange et à réduire la part des interventions curatives.
Amélioration des connaissances et savoir-faire
Il s’agit d’accroitre les compétences des opérateurs de production ainsi que des techniciens.
Sécurité, conditions de travail et environnement
C’ est le principe du zéro accident et zéro pollution.
Maitrise de la conception des produits et équipements associés
Il s’agit de capitaliser sur les erreurs du passé, de prendre en compte toutes les leçons apprises lors des résolutions de problèmes, d’intégrer les améliorations dans le design des équipements, les rendre « maintenance –free », etc.
Efficience des services connexes ou « TPM dans les bureaux »
Il s’agit de développer les contributions des services supports aux activités TPM en production, il est nécessaire d’avoir une cohérence dans le management inter et intra services.
Total Productive Management, les technologies à l'oeuvre dans l’Industrie 4.0
Les 8 piliers restent les fondamentaux de l’industrie. Mais dans le cadre d’un grand mouvement de modernisation baptisé Industrie 4.0 et sur lequel nous pouvons argumenter de la nature révolutionnaire, on peut se poser une question est simple : « en quoi cette « révolution » va venir consolider et garantir une maintenance toujours plus efficace ? ».
L’analyse de données en masse ou Big Data, l’Internet des objets, l’intelligence artificielle, la réalité virtuelle et augmentée ou encore les systèmes cyber-physiques apparaissent comme une mise à niveau numérique et autant de leviers potentiels d’amélioration.
1/ Analyse Big Data
Le terme «big data» fait référence à de grands ensembles de données techniquement complexes entrant dans les applications typiques d’analyse et de traitement de données. Cette nouvelle approche permet aux entreprises de faire de la «prédiction» à l’aide d’une analyse approfondie de grands ensembles de données qui seront activement monitorés.
On estime qu’à l’heure actuelle, la quantité d’informations stockées croît quatre fois plus vite que l’économie mondiale. Les vitesses de calcul augmentent en parallèle neuf fois plus vite. Et l’avènement de l’ordinateur quantique promet d’amplifier encore ce phénomène.
Des débuts de l'informatique jusqu'à l'année 2003, on estime que l'humanité a généré 5 exa-octets de data. L'éco-système dans lequel nous nous inscrivons aujourd'hui génère une masse équivalente de données, en seulement 2 jours.
Une étude menée auprès de 2 000 entreprises réparties dans 9 grands secteurs industriels et 26 pays montre que 80% des PDG mondiaux ont reconnu l’importance du data mining et de l’analyse pour leurs organisations.
La tendance est aujourd’hui à l’extraction de nouvelles données à partir de bases existantes. Cela fournit à l’organisation des informations techniques et commerciales importantes qui permettent une prise de décisions optimisée.
Le Cloud Computing et Cloud Manufacturing : pendants opérationnels de l’analyse Big Data
- Le Cloud Computing s’apparente à une plateforme évolutive qui aide les organisations à utiliser les ressources informatiques de manière plus rationnelle, et ouvre la voie à une automatisation des tâches poussée et une réduction des coûts générés par les systèmes isolés. Son corollaire industriel aussi appelé Cloud Manufacturing est le concept qui reflète l’idée d’une usine intelligente, c’est-à-dire la collaboration de modèles de production avancés avec la technologie informatique dans le cloud pour réaliser une production informatisée et axée sur les services (Givehchi, Tresk et Jasperneite, 2013).
2/ Internet des Objets (IoT)
L’idée de l’Internet des Objets est apparue pour la première fois dans les années 80, pour répondre aux besoins des guichets automatiques bancaires (Shon, 1996). Depuis, nombre de ces appareils ont été connectés en réseau.
Cet Internet des Objets (IoT) est la terminologie utilisée pour décrire les dispositifs physiques ou les composants qui peuvent être connectés via le réseau et ont la capacité de communiquer entre eux via des RIFD (Radio Frequency Identification) ou des capteurs intelligents (Gilchrist, 2016b).
Selon l’ISO/IEC JTC1 (2015) l’IoT est une infrastructure d’objets, de personnes, de systèmes et de ressources d’information interconnectés ainsi que des services intelligents pour leur permettre de traiter l’information du monde physique et virtuel et de réagir. Cependant, il s’agit d’un concept similaire aux systèmes cyber physiques (CPS).
Selon une estimation, environ 25 milliards d'appareils / objets seront interconnectés et auront une communication entre eux, d'ici 2020.
L’Internet des objets permet aux entreprises d’ajouter de la transparence dans les processus et de les rendre analytiquement mesurables. Ces capteurs peuvent être portés par les opérateurs, placés sur les chaines de production, sur les machines directement ou dans les entrepôts.
De même, les nouvelles solutions type RFID permettent de garantir une parfaite traçabilité des produits sur la chaine de valeur et également de mesurer la performance au quotidien grâce à la collecte de données pertinentes. La capacité des IoT à proposer une intelligence augmentée aide les entreprises à optimiser leur capacité de prise de décision, à garantir une collecte de données efficace et à générer les bons rapports pour leur environnement spécifique.
L’IoT aide l’entreprise à gagner en « intelligence », en leur donnant la capacité d’analyser leurs processus physiques qui n’étaient pas mesurables auparavant. Tout cela contribue à une meilleure capacité stratégique et opérationnelle et, dans certains cas, à un avantage concurrentiel (Kopetz, 2011).
3/ Intelligence Artificielle
L’IA a été introduite comme domaine de recherche à la fin des années 1950.
L’Intelligence Artificielle est un sous-domaine de l’informatique, dont le seul but est de donner aux machines ou aux robots une intelligence humaine telle qu’ils deviennent des plateformes indépendantes et capables de prendre des décisions intelligentes de manière autonome (McCarthy, 2007).
Il y a deux types de l’IA :
- l’intelligence artificielle mono activité (ANI) qui est liée à des applications sur une seule tâche dans un domaine très précis dont nous sommes témoins aujourd’hui (i.e. jeu Go),
- l’intelligence artificielle générale (AGI), concept large, profond et qui inclut des caractéristiques surpassant l’intelligence humaine dans de nombreuses dimensions telles que la vitesse analytique, la mémoire, le multitâche, la reconnaissance des formes et la capacité d’adaptation avec de nouvelles informations auto-apprises (Muehlhauser, 2013).
Selon Hawking et al. (2014), le succès dans la création de l’AGI serait le plus grand événement de l’histoire humaine, mais ils ne sont pas certains que ce ne soit pas aussi le dernier, à moins d’apprendre à juguler le risque, d’où la vision hésitante des experts par rapport à l’IA.
Combien d’emplois seront remplacés par les robots et l’IA dans les prochaines années ? Et combien de nouveaux métiers et postes seront-t-ils créées ? La réponse n’est pas donnée, mais pour illustrer, la plus grande banque du Japon, Mitsubishi UFJ Finance, a récemment installé des robots pour ses opérations de service client et l’IPsoft, un centre d’appel, utilise un robot d’IA « Amelia » capable d’auto-apprendre en dehors des connaissances préprogrammées. « Amelia » peut maintenant traiter plus de 60% de toutes les requêtes entrantes.
4/ Réalité virtuelle et augmentée
L’usine intelligente sera aidée par des programmes avancés de ressources humaines en « réalité virtuelle et réalité augmentée ». La réalité virtuelle (VR) est un environnement simulé par ordinateur. Elle est présentée à l’utilisateur comme un environnement réel. Elle peut aider les programmes de formation des employés et dans l’assistance aux processus opérationnels à l’aide d’appareils numériques compatibles. En revanche, la réalité augmentée (AR) a une longueur d’avance et permet à l’utilisateur d’interférer avec un environnement simulé (Boud et al., 1999). Selon Jason Ganz, PDG d’Agora VR « Internet nous a permis d’apprendre quoi que ce soit – VR et AR nous permettront de tout expérimenter ». Les experts suggèrent que certaines des tâches de management se tiendront virtuellement comme par exemple les réunions et les conférences stratégiques. De plus la VR et l’AR aideront le département des ressources humaines dans la formation et le système d’accompagnement continu pour la transition dans un environnement numérique.
5/ Systèmes cyber-physiques
Afin de rendre l’usine intelligente opérationnelle ou fonctionnelle, nous aurons besoin des « Systèmes Cyber Physiques (CPS) ». Les CPS sont des systèmes intelligents qui permettent de créer un pont entre les composants virtuels et physiques utilisés dans la production, la logistique et les produits. C’est le concept qui se combine avec l’Internet des Services (IoS) pour rendre l’industrie 3.X possible, ce qui ouvre de nouvelles possibilités pour des applications et processus innovants. Les CPS faciliteront le changement de paradigme par rapport aux « business models » et « market models » avec tous les intervenants de la chaine de valeur y compris les fournisseurs. Toutes ces technologies combinées à d’autres technologies telles que la fabrication additive, par exemple l’impression 3D, le frittage sélectif par laser, la cobotique, l’AGV, etc., constituent les bases pour l’usine du futur, qui regroupe des systèmes virtuels et physiques via des systèmes cyber physiques. Une telle fusion des processus techniques et des processus d’affaires fera une porte d’entrée au concept connu sous le nom de « Smart Factory » (MacDougall, 2014).
Ces technologies existent. Il convient à présent de s’interroger comment elles contribuent aux sites de production d’aujourd’hui. Dans le cadre de démarches de TPM, les contributions de l’environnement numérisé offre déjà des solutions pratiques que nous mettons en place chez nos clients.
Sources :
Boud, A. C., Haniff, D. J., Baber, C., & Steiner, S. J. (1999). Virtual reality and augmented reality as a training tool for assembly tasks. In Information Visualization, 1999. Proceedings. 1999 IEEE International Conference on (pp. 32-36). IEEE.
Gilchrist, A. (2016b). Middleware Industrial Internet of Things Platforms. In Industry 4.0 (pp. 153-160). Apress.
Givehchi, O., Trsek, H., & Jasperneite, J. (2013). Cloud computing for industrial automation systems—A comprehensive overview. In Emerging Technologies & Factory Automation (ETFA), 2013 IEEE 18th Conference on (pp. 1-4). IEEE.
Hawking, S., Russell, S., Tegmark, M., & Wilczek, F. (2014). Stephen Hawking: \’Transcendence looks at the implications of artificial intelligence-but are we taking AI seriously enough?’. The Independent, 2014(05-01), 9313474
Kopetz, H. (2011). Internet of things. In Real-time systems (pp. 307-323). Springer US.
Shon, S. W. (1996). U.S. Patent No. 5,499,238. Washington, DC: U.S. Patent and Trademark Office.
MacDougall, W. (2014). Industrie 4.0: Smart manufacturing for the future. Germany Trade & Invest.
McCarthy, J. (2007). WHAT IS ARTIFICIAL INTELLIGENCE? Retrieved March 15, 2017, from http://www-formal.stanford.edu/jmc/whatisai/
Muehlhauser, L. (2013, September 15). What is AGI? Retrieved March 26, 2018, from https://intelligence.org/2013/08/11/what-is-agi/